Many industrial sites still operate boilers that were commissioned in the last century. These boilers often use traditional analog control or early relay logic control systems, which struggle to meet modern safety and efficiency requirements. When upgrading boilers, achieving seamless integration between old and new control systems is crucial. The transition must be smooth to avoid production disruptions while ensuring the new control system is fully compatible with existing equipment to maximize efficiency.
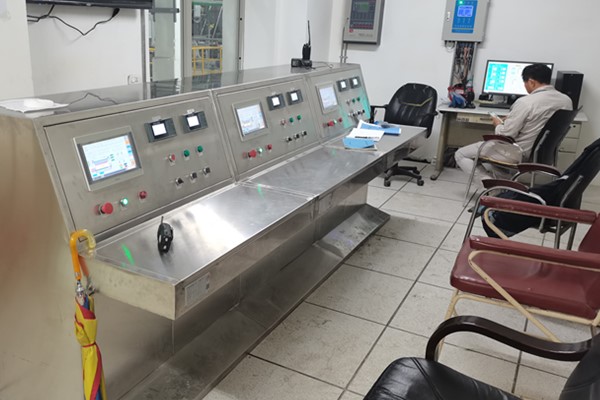
With extensive experience in system retrofitting and a comprehensive service framework, Henan Rentai Electrical Equipment Co., Ltd. ensures smooth hardware and software integration during boiler control upgrades. This guarantees the new system is quickly commissioned, operates reliably, and enhances boiler performance.
Urgency of Upgrading Old Boiler Control Systems
With stricter environmental and safety regulations, many old boilers urgently require modernization. In 2023, China had approximately 800,000 industrial boilers, with over 60% classified as outdated and in need of upgrades. Policies mandate that coal-fired boilers comply with stricter emission standards by 2025, driving industries to accelerate retrofits.
At the same time, modern PLC and DCS control systems significantly improve boiler efficiency, automation, and reliability, reducing manual operation requirements. The boiler retrofitting market reached 120 billion RMB in 2023, growing 15% annually, and is projected to expand to 150 billion RMB by 2025. However, seamlessly transitioning from old to new control systems poses technical challenges. Companies must protect their existing investments while migrating to modern platforms. Older boiler control systems typically use relay-contactor circuits, analog instrumentation panels, or early-generation PLCs with limited automation and lower reliability. Some aging power plants still operate gauge-based control panels with manual switches instead of computer-based monitoring.
Transitioning to digital PLC-based control can lead to signal incompatibility, missing safety interlocks, or operational difficulties for personnel if not handled properly. A well-planned approach is essential to ensure smooth system migration and seamless integration of new and old systems.
Technical Strategies for Seamless System Integration
To successfully integrate legacy boiler control systems with modern systems, strategies must be implemented at both hardware and software levels.
1. Signal Compatibility and Interface Integration
The first step is analyzing all sensors, actuators, and control loops in the old system to determine: Which components can be retained/Which need replacement or upgrades. Typically, existing pressure, temperature, and level transmitters can be reused if they remain accurate and reliable, while old relay logic can be replaced with new PLC programming to maintain functional equivalence. If necessary, protocol converters or signal conditioning modules can bridge old and new systems. For example, some legacy systems use 4-20mA analog signals or Modbus communication, requiring appropriate I/O modules or communication interfaces in the new PLC. Additionally, all critical safety interlocks (e.g., low water level shutdown, overpressure trip) must be recreated or enhanced in the new system to maintain boiler safety.
Henan Rentai emphasizes signal compatibility in its retrofitting projects. Engineers thoroughly test legacy sensors and actuators, select appropriate I/O modules, and, if needed, add signal conditioning units to ensure seamless communication between old equipment and the new PLC. For instance, in a boiler upgrade project, the existing furnace pressure gauge output a 0-10V signal, but the new PLC only supported 4-20mA inputs. Henan Rentai engineers implemented a signal conversion module, successfully integrating furnace pressure into the PLC for closed-loop control, ensuring a smooth and reliable transition.
2. Retaining and Optimizing Control Logic
Older control systems contain years of operational experience in their logic. The new system should inherit proven control sequences and interlock relationships to ensure smooth operation. Henan Rentai engineers extract and analyze old control schematics or programs, then reimplement them in the new PLC/DCS. This ensures that boiler operation remains familiar to plant personnel, facilitating adoption. At the same time, the new system allows performance improvements, such as: Replacing manual adjustments with PID control/Adding new functions like automatic soot blowing or load forecasting. However, these enhancements are introduced gradually to avoid disrupting continuity.
For example, in an old oil-fired boiler upgrade, the existing three-element combustion control strategy was retained to stabilize the water level. However, Henan Rentai also added oxygen monitoring and combustion optimization, improving efficiency while maintaining operational consistency. This "inheritance + optimization" approach ensures a seamless transition while leveraging new technology advantages.
3. Parallel Testing and Switchover Strategy
To minimize production disruptions, new and old systems can be run in parallel before the final switchover. Henan Rentai follows a structured approach: Factory Acceptance Testing (FAT): A replica control system is built and tested in the lab before deployment. On-Site Installation: The new control cabinet and PLC are installed while the old system remains operational. Data Validation: The new system monitors critical parameters, but control remains with the old system. Seamless Transition: Once signals match and control outputs are validated, a planned switchover is executed. Switchover is typically performed during scheduled maintenance or low-demand periods to minimize downtime. In some cases, Henan Rentai adopts a phased upgrade approach, first upgrading combustion control, then feedwater systems, ensuring stability at each stage. This approach allows for a smooth transition with minimal disruption to operations.
4. Operator Training and Interface Adaptation
Old systems rely on gauge displays and manual switches, while new systems feature HMI touchscreens and computer monitoring. This presents a learning curve for operators.
To ensure smooth adaptation, Henan Rentai provides on-site training covering: HMI operation/Report generation and alarm handling/Differences from the old system/Simulated boiler startup, shutdown, and emergency scenarios are conducted before the new system goes live. This ensures that operators feel confident using the new system from day one. To further ease the transition, HMI layouts are customized to resemble the logical arrangement of the old control panel. Key emergency buttons, such as shutdown switches, remain physical buttons to prevent accidental touchscreen operations. These user-focused design adjustments help reduce the operator's learning curve and facilitate a seamless transition to modern control.
Henan Rentai's Expertise in Boiler Control Upgrades
As a leading industrial boiler control systems integrator, Henan Rentai offers:
Experienced technical teams: Engineers proficient in modern PLC/DCS control and legacy systems, ensuring a deep understanding of both old and new technologies.
Comprehensive project services: Covering consultation, site assessment, system design, installation, commissioning, and training for turnkey upgrades.
Strong project track record: Proven success in seamless boiler control system upgrades, backed by highly satisfied clients.
Benefits of Boiler Control System Upgrades
By seamlessly upgrading old boiler control systems, industries benefit from:
Increased Efficiency & Energy Savings: Modern control algorithms reduce fuel consumption and optimize combustion. Adding oxygen control alone can cut fuel costs by 2-5% annually.
Enhanced Safety & Reliability: Advanced interlocks and self-diagnostic features reduce accident risks. Henan Rentai’s emergency shutdown circuits and UPS backup power ensure safety even during power failures.
Extended Equipment Lifespan: Upgrades prolong boiler life by 5-10 years, avoiding costly new boiler investments.
Smart Monitoring & IoT Integration: Upgraded systems enable real-time remote monitoring via SCADA or mobile apps, improving operational transparency and efficiency.
With boiler retrofitting demand surging, Henan Rentai continues to innovate and deliver cost-effective, high-performance control upgrades, driving the industry towards intelligent and sustainable operations.
?? Contact Henan Rentai Electrical:
Phone: +86-17638563962 / +86-0371-56520104
Email: info@hnrentai.com